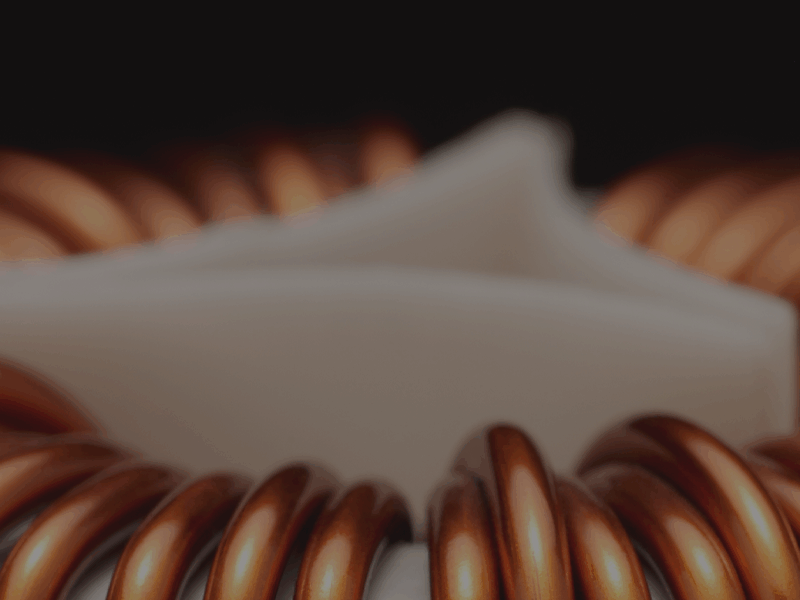
From Copper to Core: The Precision Behind High-Performance EV Motors
Introduction
When people talk about the electric vehicle (EV) revolution, they often focus on batteries, charging infrastructure, or stylish car designs. Yet, hidden beneath the hood of every EV is a marvel of engineering that truly brings the vehicle to life: the electric motor. At the core of these motors lies a coil winding, a process that is both art and science. In recent years, the evolution of winding machines has quietly but profoundly transformed EV motor manufacturing.
With an emphasis on precision, efficiency, and sustainability, these machines are enabling automakers to build motors that are not only more powerful but also more environmentally friendly. This blog explores how advanced winding machines are reshaping the landscape of EV manufacturing and why their impact is pivotal for the future of transportation.
The Critical Role of Precision in EV Motor Manufacturing
The electric motor is the heart of any EV, converting electrical energy into mechanical motion. The performance, efficiency, and longevity of these motors depend largely on the quality of their internal coils. Traditionally, coil winding was a manual process, prone to inconsistencies and human error. Today, automated winding machines have taken centre stage, delivering levels of precision that were once unimaginable.
Precision in coil winding is crucial for several reasons. First, it ensures that the copper or aluminium wire is wound tightly and uniformly. This will maximize the magnetic field strength and minimize electrical resistance. This directly translates to higher motor efficiency and better energy utilization, which are essential for extending the driving range of EVs. Secondly, precise winding reduces the risk of hot spots and insulation failures, improving the durability and safety of the motor. Finally, consistent coil geometry allows for better thermal management, enabling motors to operate at higher power levels without overheating.
From Manual to Automated Excellence
The shift from manual to automated winding represents one of the most significant advancements in EV motor manufacturing. Modern winding machines are equipped with sophisticated controls, sensors, and robotics. They ensure that every coil is produced to exact specifications. Techniques such as hairpin winding, distributed winding, and wave winding have emerged as industry standards, each offering unique benefits for EV motors.
Hairpin winding uses pre-formed rectangular copper bars, bent into U-shapes and inserted into the stator slots. These hairpins are then laser-welded to form continuous coils. This method allows for a higher copper fill factor up to 70% compared to 45–50% with traditional round wire, resulting in greater power density and improved heat dissipation. The increased slot fill not only boosts motor performance but also contributes to more compact and lightweight designs, which are critical for EVs.
Distributed winding and wave winding further enhance efficiency by optimizing the distribution of the magnetic field within the motor. Automated machines can switch between these winding patterns with minimal setup time, offering manufacturers the flexibility to produce motors tailored to different vehicle models and performance requirements.
How Automation Drives Efficiency and Quality?
Automation in winding machines delivers several key advantages for EV manufacturing. First, it drastically reduces the cycle time for coil production, enabling high-volume output without sacrificing quality. Advanced machines can wind, insert, and weld coils with micron-level accuracy, ensuring that every motor meets stringent industry standards.
Second, automation minimizes material waste. Precise control over wire tension and placement means less scrap and fewer defects, which is both economically and environmentally beneficial. In an industry where copper prices are volatile and sustainability is a growing concern, reducing waste is a significant advantage.
Third, automated winding machines are equipped with real-time monitoring and quality control systems. Sensors track parameters such as wire tension, temperature, and alignment, immediately flagging any deviations from the set specifications. This allows for instant corrections, reducing the likelihood of defective motors reaching the assembly line.
Sustainability: Building Greener Motors for a Cleaner Future
Sustainability is at the forefront of the EV movement, and winding machines play a critical role in advancing this goal. By maximizing material utilization and minimizing waste, these machines help manufacturers reduce their environmental footprint. Many modern winding machines are designed with energy efficiency in mind, consuming less power during operation and supporting the use of recycled materials.
In addition, the precision offered by automated winding machines enables the use of alternative materials such as aluminium, which is lighter and more abundant than copper. While aluminium is less conductive, advanced winding techniques can compensate for this, making it a viable option for certain EV applications. The ability to experiment with and adopt new materials is essential for the long-term sustainability of EV manufacturing.
Manufacturers are also exploring closed-loop recycling systems, where scrap wire and defective coils are collected, processed, and reused in new production cycles. This not only conserves resources but also aligns with the circular economy principles that are increasingly important in the automotive industry.
Overcoming Manufacturing Challenges with Winding Solutions
Despite the many benefits, implementing advanced winding machines in EV manufacturing is not without challenges. The initial investment in automation technology can be substantial, especially for smaller manufacturers. Training workers to operate and maintain these sophisticated machines requires time and resources.
However, the long-term benefits far outweigh the costs. Automated winding machines reduce labour requirements, lower defect rates, and enable manufacturers to scale production quickly in response to market demand. As the technology continues to evolve, costs are expected to decrease, making advanced winding solutions accessible to a broader range of manufacturers.
The Human Element
While automation is transforming the manufacturing landscape, human expertise remains invaluable. Technicians and engineers are needed to program, monitor, and maintain winding machines, as well as to innovate new winding techniques. Many companies are investing in training programs to upskill their workforce, ensuring that employees can thrive in an increasingly automated environment.
Collaboration between machine operators, engineers, and quality control specialists is essential for optimizing production processes. Also, it helps in achieving the highest standards of precision and efficiency. By implementing a culture of continuous learning and innovation, manufacturers can stay ahead in the competitive EV market.
The Future of Precision Winding in EVs
The future of EV motor manufacturing will be defined by continued advancements in winding technology. Artificial intelligence and machine learning are poised to play a larger role, enabling machines to self-optimize winding patterns and predict maintenance needs. The integration of IoT devices will provide real-time data on machine performance, further enhancing efficiency and reliability.
Sustainability will remain a driving force, with ongoing efforts to develop recyclable materials, reduce energy consumption, and minimize waste. As the industry moves toward greater electrification, the demand for high-precision, sustainable winding solutions will only grow.
Conclusion
Winding machines are at the heart of the EV revolution, enabling manufacturers to build motors that are powerful, efficient, and sustainable. Through advancements in automation, precision engineering, and material utilization, these machines are helping to shape a cleaner, greener future for transportation.
As technology continues to evolve, the role of winding machines in EV manufacturing will become even more central. This in return drives innovation and setting new standards for performance and environmental responsibility. The next time you see an electric vehicle glide silently by, remember that its smooth, efficient motion is made possible by the unseen work of precision winding machines.